In the dynamic landscape of material handling, the term "stacker" encompasses a diverse range of equipment designed primarily for the vertical movement and storage of goods. From small, pedestrian-operated units to massive, automated cranes, stackers play a pivotal role in optimizing warehouse space, improving efficiency, and ensuring safe operations. While often confused with general forklifts, stackers are a specialized subset characterized by their emphasis on high-density vertical stacking capabilities.
The question "How many types of stacker are there?" doesn't have a single, simple numerical answer because the classification can be approached from several angles: by power source, by operator position, by mast design, by primary application, and by level of automation. However, by exploring these different categories, we can develop a comprehensive understanding of the vast array of stackers available, highlighting their distinct features and applications. It's important to note that while some forklifts, such as a DIESEL FORKLIFT or ROUGH TERRAIN TRUCKS, can indeed stack, they are typically classified more broadly as "forklifts" due to their primary design for general transport and varied lifting tasks, whereas "stackers" are specifically optimized for vertical storage within more confined or structured environments.
Let's break down the main types of stackers:
I. Classification by Power Source:
Manual Stackers:
Description: These are the most basic and economical stackers. They rely on manual pumping for hydraulic lift and human effort for propulsion and steering.
Characteristics: Limited lift height (typically 60-100 inches), low capacity (up to 1-1.5 tons), slow speed.
Application: Ideal for very light-duty, infrequent lifting and short-distance transport in small storerooms, retail backrooms, or as a backup unit. Reduces physical strain compared to manual lifting.
Semi-Electric Stackers:
Description: Combine manual propulsion and steering with an electric motor for powered lifting. A battery powers the hydraulic pump.
Characteristics: Improved lifting speed and ease compared to manual. Still relies on operator for movement.
Application: Suitable for medium-duty tasks where repetitive lifting is common but long-distance travel is not. Bridges the gap between manual and fully electric models.
Fully Electric Stackers (Powered Pallet Stackers):
Description: Utilize electric motors for both lifting and propulsion, powered by a battery (lead-acid or lithium-ion). These are the most common type of stacker in modern warehouses.
Characteristics: Significant reduction in operator fatigue, faster cycle times, precise control. Quiet operation and zero emissions make them suitable for indoor use.
Application: Versatile for a wide range of indoor applications, from small warehouses to large distribution centers, for stacking in racks, loading/unloading trucks, and short-to-medium distance transport.
I. Classification by Operator Position:
Walkie Stackers (Pedestrian Stackers):
Description: The operator walks behind or beside the machine, guiding it via a tiller arm. They are typically compact and highly maneuverable.
Characteristics: Simple to operate, excellent for tight aisles and limited spaces. Lower travel speeds. OSHA Class III.
Application: Small warehouses, retail stores, loading docks, and areas where space is a premium. Often used for light to medium-duty stacking tasks.
Rider Stackers (Stand-on / Ride-on Stackers):
Description: Equipped with a platform or a small compartment where the operator stands or sits while operating the machine.
Characteristics: Allow for faster travel speeds over longer distances, reducing operator fatigue. More productive for higher-volume operations. Can sometimes be classified as Class I (electric motor rider trucks) or Class III depending on specific design.
Application: Medium to large warehouses with longer travel paths, high-density racking, and operations requiring a balance of vertical stacking and horizontal transport.
III. Classification by Mast and Load Handling Mechanism:
This is where the functional design of the stacker significantly differentiates them.
Standard Walkie / Counterbalance Stackers:
Description: These stackers use a counterweight in their chassis to offset the load weight, similar to a standard counterbalance forklift but in a more compact, often walk-behind design. The forks extend directly from the front of the machine.
Characteristics: Can pick up and place any type of pallet (open or closed bottom) as there are no straddle legs to interfere. Require wider aisles than straddle stackers due to their longer overall length.
Application: Versatile for handling various pallet types and in environments where wider aisles are available, or where accessing loads close to walls/machinery is necessary.
Walkie Straddle Stackers:
Description: Characterized by "straddle" legs that extend forward from the main chassis and go around the pallet being lifted. The forks are positioned between these legs.
Characteristics: Highly stable due to the load being embraced by the legs. Can handle both open and closed-bottom pallets. Require less aisle width than counterbalance stackers but need clearance for the straddle legs.
Application: Very popular in warehouses with selective racking systems. Their design allows for efficient high-density stacking in relatively narrow aisles.
Walkie Reach Stackers (Pantograph Reach Stackers):
Description: Similar to straddle stackers but equipped with a pantograph mechanism (scissor-like reach mechanism) that allows the mast and forks to extend forward beyond the outrigger legs.
Characteristics: Can pick up and place loads deep into racking (e.g., double deep racking) without needing to drive the entire machine into the rack. Provides excellent stability.
Application: Ideal for maximizing storage density by utilizing double-deep racking. Often used in cold storage or highly organized warehouses where space is at a premium. They act as a more compact alternative to full-sized reach trucks for certain applications.
Fork-Over Stackers:
Description: Designed with forks that sit over two narrow straddle legs. The forks go under the load.
Characteristics: Can only be used with open-bottom pallets, skids, or specialized containers (e.g., Europallets, GKN pallets, or two-way entry pallets where the bottom boards allow the legs to pass underneath). Very compact.
Application: Common in operations exclusively using open-bottom pallets or skids, offering a highly maneuverable and economical stacking solution.
IV. Classification by Specialization/Application:
Container Reach Stackers (e.g., MYCQDA Reach Stacker from previous article):
Description: A highly specialized, massive piece of heavy equipment used in intermodal terminals, ports, and large logistics hubs. They have a telescopic boom and a spreader attachment to handle large shipping containers.
Characteristics: Immense lifting capacities (tens of tons), ability to stack containers multiple high and multiple deep, designed for outdoor, heavy-duty use. These are not "forklifts" in the traditional sense, but rather a distinct type of "stacker" for containers.
Application: Essential for high-density container storage and movement in global shipping and logistics operations.
Order Pickers (Low, Medium, and High-Level):
Description: While not always explicitly called "stackers," order pickers are machines designed for operators to be lifted to various rack heights to manually pick individual items or cases from shelves. Some models have forks to lift a pallet, but their primary function is picking.
Characteristics: Operator lifts with the platform, often very narrow aisle (VNA) capable. Can reach significant heights.
Application: Warehouses with high-level shelving for piece or case picking, typically integrated with warehouse management systems.
Automated Storage and Retrieval Systems (AS/RS) Stacker Cranes:
Description: These are fully automated machines that travel on fixed rails within specialized racking systems. They lift, retrieve, and put away loads (pallets, cartons, totes) without human intervention, controlled by software.
Characteristics: Extremely high density, speed, and accuracy. Operate 24/7. Can operate in lights-out facilities or extreme environments (e.g., cold storage).
Types of Stacker Cranes: Single-mast, double-mast (for heavier loads/higher lifts), mini-load (for small items), satellite (for deep-lane storage).
Application: High-throughput distribution centers, automated factories, and where space is extremely limited or labor is expensive.
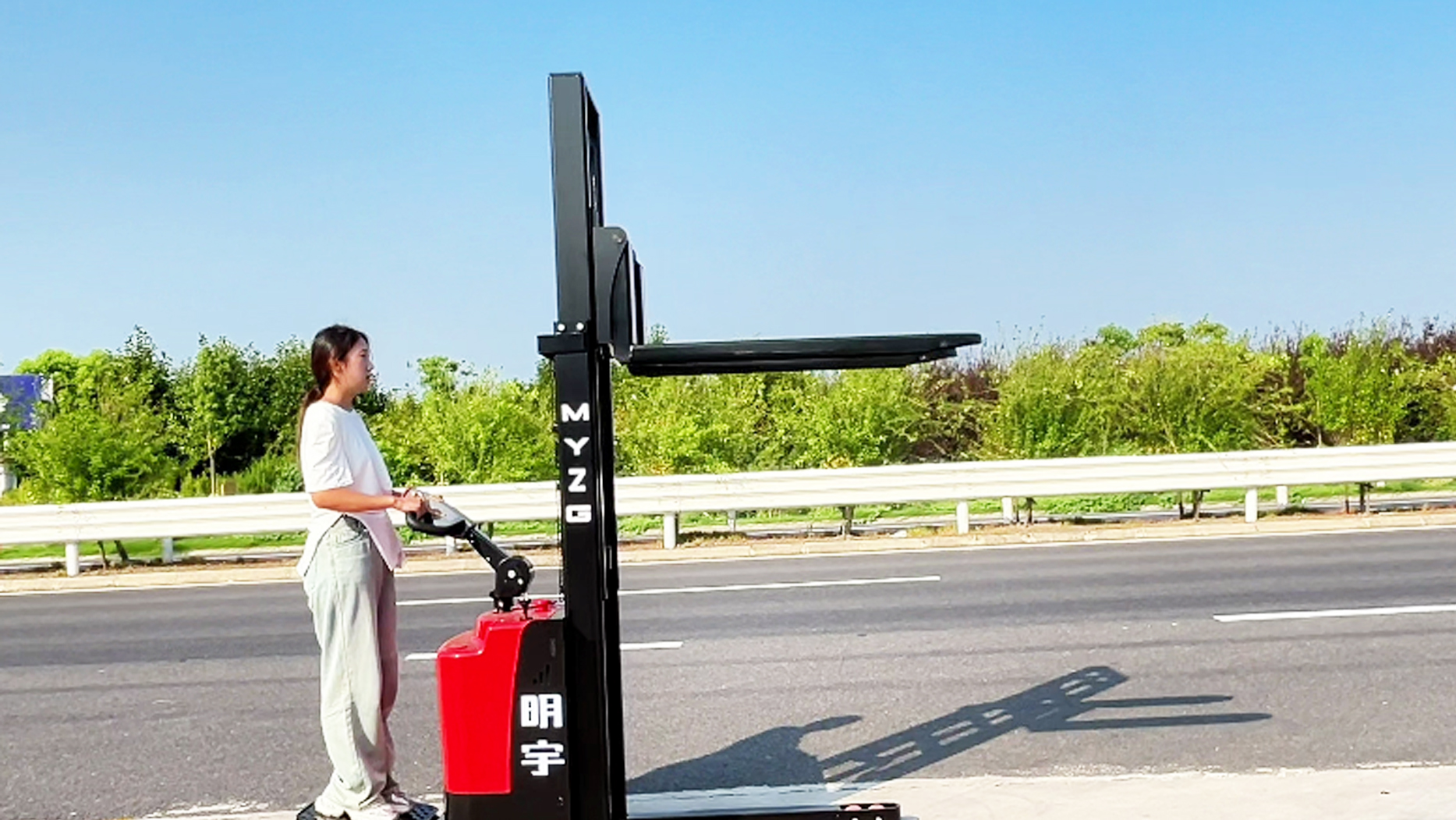
V. The Forklift Family (Contextual Clarification):
It's crucial to understand that while all stackers are powered industrial trucks capable of stacking, not all forklifts are "stackers" in the narrow definition of optimizing vertical storage in compact areas. OSHA categorizes forklifts into seven classes:
Class I: Electric Motor Rider Trucks (includes electric counterbalance forklifts, some electric rider stackers)
Class II: Electric Motor Narrow Aisle Trucks (includes reach trucks, order pickers, turret trucks, often considered advanced stackers or narrow-aisle forklifts)
Class III: Electric Motor Hand or Hand/Rider Trucks (includes walkie stackers, walkie pallet jacks)
Class IV: Internal Combustion Engine Trucks (Cushion Tires) (e.g., some compact DIESEL FORKLIFT models used indoors with exhaust scrubbers, though less common)
Class V: Internal Combustion Engine Trucks (Pneumatic Tires) (the most common type of DIESEL FORKLIFT and gas/LPG forklifts for outdoor/heavy duty use)
Class VI: Electric and Internal Combustion Engine Tractors (Tuggers/Tow Tractors)
Class VII: Rough Terrain Forklift Trucks (e.g., ROUGH TERRAIN TRUCKS or telehandlers)
While a DIESEL FORKLIFT (often Class IV or V) can stack, its primary design isn't solely for tight-aisle vertical optimization like many electric stackers. It's built for power, outdoor use, and varied lifting tasks. Similarly, ROUGH TERRAIN TRUCKS (Class VII) are designed for challenging outdoor environments and can stack to significant heights (especially telehandlers), but they are specialized for terrain rather than being part of the "stacker" family primarily focused on high-density warehouse racking. They belong to the broader forklift classification.
Conclusion: A Spectrum of Vertical Solutions
In conclusion, there isn't a fixed number for "how many types of stacker are there," as the categorizations overlap and new designs emerge. However, by understanding the distinctions based on power (manual, semi-electric, fully electric), operator position (walkie, rider), load handling mechanism (counterbalance, straddle, reach, fork-over), and specialization (container, order picker, automated), we can identify at least ten distinct types of stackers, with numerous sub-variants and specific models within each.
From the simple, cost-effective manual stacker to the highly sophisticated automated stacker crane, and the specialized Container Reach Stacker that manages global trade, stackers represent a critical family of equipment dedicated to maximizing vertical storage and streamlining material flow. While the DIESEL FORKLIFT and ROUGH TERRAIN TRUCKS are powerful lifting machines, their classification differs due to their primary design for general outdoor or heavy-duty transport and lifting, distinct from the focused vertical optimization that defines the diverse world of true "stackers."
Post time:May.23.2025